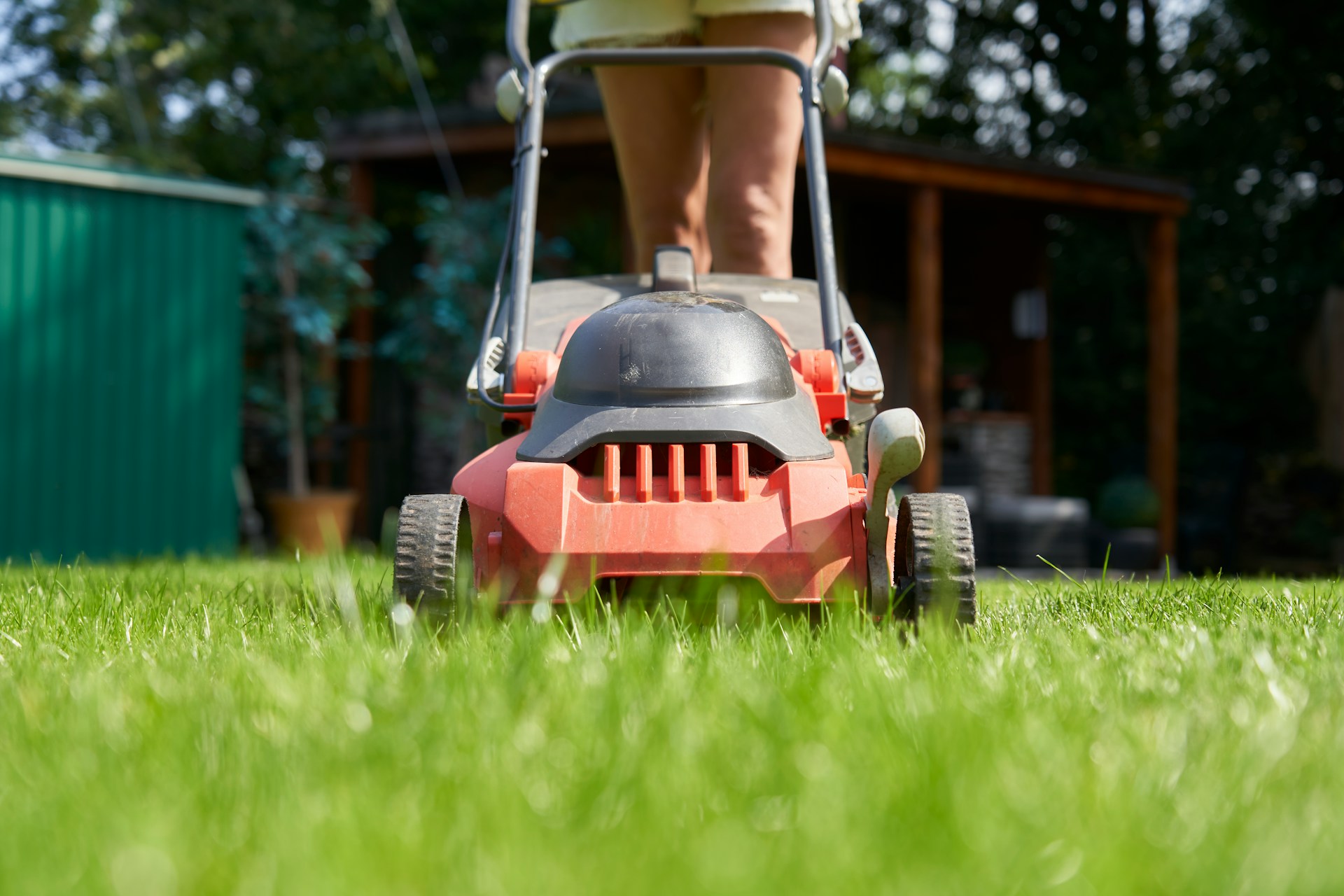
Proper seasonal maintenance determines whether your small engine equipment starts reliably when you need it most.
From spring lawn mower preparation to winter storage procedures, following systematic maintenance routines extends equipment longevity and prevents costly breakdowns during peak usage periods.
Many equipment owners overlook critical maintenance steps that could save hundreds in repair costs and prevent frustrating equipment failures. Professional maintenance doesn’t require advanced mechanical skills—just consistent attention to key components and proper timing of service intervals.
This comprehensive maintenance checklist covers essential procedures for all seasons, helping you maintain peak performance from lawnmowers to snow blowers, generators to chainsaws.
Whether you’re preparing equipment for heavy use or storing it for off-seasons, these proven maintenance practices will keep your engines running smoothly year after year.
Spring Preparation and Startup Procedures
Spring signals the start of heavy equipment use for many homeowners, but after months in storage, engines need proper preparation to ensure dependable operation throughout the growing season.
A well-maintained fuel system is key to avoiding common springtime issues and promoting equipment longevity.
Begin by inspecting the fuel tank for signs of water contamination, sediment buildup, or fuel degradation. Stale fuel is a leading cause of hard starts, rough idling, and performance issues.
Completely drain any old fuel from the tank and replace it with fresh gasoline that meets the manufacturer’s specifications. For added protection during extended storage, mix in a fuel stabilizer—even with fresh fuel.
Next, check fuel lines for cracks, leaks, or signs of wear. Cold winter temperatures can make rubber fuel lines brittle and prone to leaks, posing both fire hazards and risks of fuel system contamination. Replace any damaged fuel lines before putting your equipment to work, ensuring safe and efficient operation while extending its lifespan.
With thorough preparation, you can keep your equipment in top shape and enjoy reliable performance season after season.
Oil System Inspection and Changes
Fresh oil protects internal engine components from wear and corrosion during startup after storage. Check oil level and condition before first spring use. Dark, thick oil or oil containing metal particles indicates the need for immediate replacement.
Change oil and oil filters according to manufacturer specifications, typically every 25-50 hours of operation or annually. Use oil viscosity appropriate for expected operating temperatures. Multi-viscosity oils like 10W-30 work well for most small engines in moderate climates.
Clean oil fill areas thoroughly before adding new oil to prevent contamination. Dispose of used oil properly at recycling centers or auto parts stores that accept waste oil.
Air Filter Maintenance and Replacement
Clean air filters ensure proper fuel mixture and prevent engine damage from dust and debris. Remove air filter covers and inspect filter elements for dirt accumulation, tears, or oil saturation.
Paper air filters require replacement when dirty or damaged. Foam filters can be cleaned with warm soapy water, dried completely, and re-oiled with appropriate filter oil. Pre-filters should be cleaned or replaced during air filter service.
Equipment operating in dusty conditions requires more frequent air filter service. Check filters every 10-25 hours of operation or monthly during heavy use periods.
Summer Maintenance and Peak Season Care
Summer represents the peak operating season for most small engines, requiring increased attention to cooling systems, fuel quality, and component wear. Hot weather operation stresses engines and accelerates component degradation.
Monitor engine temperatures during operation. Excessive heat can cause permanent damage to internal components and reduce engine life significantly. Clean cooling fins regularly to maintain proper airflow around the engine.
Check and clean debris from engine shrouds and air intake screens. Grass clippings, leaves, and dirt can restrict airflow and cause overheating. Remove buildup after each use in heavy debris conditions.
Fuel System Summer Considerations
Summer heat accelerates fuel degradation and increases evaporation in fuel tanks. Check fuel levels regularly and keep tanks at least half full to minimize condensation. Add fuel stabilizer to extend fuel life during hot weather storage.
Inspect fuel caps and venting systems for proper operation. Clogged or damaged fuel caps can create vacuum conditions that prevent proper fuel flow. Clean venting holes and replace damaged caps promptly.
Check carburetor adjustment if engine performance changes during hot weather. High temperatures can affect the fuel mixture and require minor adjustments for optimal performance.
Cooling System Maintenance
Clean cooling fins and shrouds weekly during heavy use periods. Use compressed air or soft brushes to remove debris without damaging delicate fin structures. Bent cooling fins reduce cooling efficiency and can cause overheating.
Check engine oil levels more frequently during hot weather operations. High temperatures increase oil consumption and accelerate oil breakdown. Top off oil levels as needed and change oil more frequently if operating in extreme conditions.
Monitor belt tension and condition on equipment with driven accessories. Heat and heavy use can cause belt stretching and premature wear. Adjust tension according to manufacturer specifications.
Fall Preparation and Storage Setup
Fall maintenance prepares equipment for winter storage while addressing wear from summer operations. Proper fall preparation prevents costly spring repairs and ensures reliable startup after storage periods.
Perform thorough cleaning of all equipment before storage. Remove grass clippings, leaves, and debris that can retain moisture and cause corrosion. Clean and dry all surfaces before applying protective treatments.
Change engine oil before storage to remove contaminants and combustion byproducts that can cause internal corrosion. Fresh oil provides better protection during storage periods than used oil.
Fuel System Preparation for Storage
Fuel system preparation prevents most storage-related problems. Add fuel stabilizer to a nearly full tank and run the engine for 10-15 minutes to distribute stabilizer throughout the fuel system.
Some manufacturers recommend draining fuel systems completely for storage. Consult equipment manuals for specific recommendations. If draining fuel, run the engine until it stops from fuel starvation to clear carburetor passages.
Remove and clean fuel filters before storage. Install new filters if existing ones show signs of contamination or restricted flow. Clean fuel systems prevent spring startup problems.
Battery and Electrical System Care
Remove batteries from equipment stored in unheated areas. Clean battery terminals and apply a protective coating to prevent corrosion. Store batteries in cool, dry locations and charge monthly to prevent sulfation.
Check spark plugs and replace them if electrodes show excessive wear or deposits. Clean spark plug threads and apply an anti-seize compound before installation. Properly gapped spark plugs improve cold weather starting.
Inspect wiring for damage from rodents or weather exposure. Protect vulnerable wiring with appropriate covers or conduits. Replace damaged wiring before storage to prevent electrical problems.
Winter Storage and Cold Weather Considerations
Proper winter storage protects equipment from cold weather damage and moisture-related problems. Cold temperatures can cause component failures and fuel system issues that are preventable with proper preparation.
Store equipment in dry, ventilated areas when possible. Avoid areas with temperature extremes or high humidity that can cause condensation and corrosion. Cover equipment with breathable materials rather than plastic tarps that trap moisture.
Position equipment to prevent moisture accumulation in cylinders and fuel systems. Store engines with cylinders in horizontal positions when possible to prevent oil migration into combustion chambers.
Cold Weather Starting Procedures
Cold weather starting requires modified procedures to ensure reliable operation. Allow engines to warm up gradually before applying heavy loads. Cold oil provides less lubrication protection than warm oil.
Use appropriate oil viscosity for cold weather operations. Single-grade oils may be too thick for cold starting, while multi-viscosity oils flow better at low temperatures. Consult manufacturer recommendations for extreme cold conditions.
Pre-warm engines in heated areas when possible for easier starting. Block heaters or heated storage areas reduce starting effort and extend engine life in cold climates.
Professional Service and Dealer Support
Regular professional service complements owner maintenance and addresses complex repairs beyond typical homeowner capabilities. Establish relationships with qualified service providers before equipment problems occur.
Professional technicians can perform carburetor rebuilds, valve adjustments, and internal engine repairs that require specialized tools and training. Annual professional service often prevents major failures and extends equipment life.
When researching service options, pwc dealers near me often provide excellent small engine service capabilities, as they regularly service marine engines with similar maintenance requirements.
These professionals understand seasonal maintenance needs and can provide valuable insights into local operating conditions.
Warranty and Service Documentation
Maintain detailed service records for warranty purposes and resale value. Document all maintenance procedures, part replacements, and service dates. Good records help diagnose problems and prove proper maintenance for warranty claims.
Keep original purchase receipts and warranty information in accessible locations. Register equipment with manufacturers for warranty coverage and service notifications. Some manufacturers offer extended warranty options for equipment receiving regular professional service.
Parts Availability and Inventory Management
Stock common replacement parts and consumables for uninterrupted equipment operation. Air filters, spark plugs, oil, and fuel filters should be available for routine maintenance without delays.
Purchase parts from authorized dealers to ensure proper fit and quality. Generic parts may appear similar but can cause performance problems or void warranties. Genuine parts typically offer better reliability and longer service life.
Store parts in clean, dry conditions to prevent deterioration. Label parts clearly with equipment model numbers and installation dates. Rotate stock to use older parts first and prevent age-related failures.
Troubleshooting Common Issues
Develop systematic approaches to diagnose common problems before they require professional service. Many starting, running, and performance issues stem from maintenance neglect rather than component failures.
Keep basic troubleshooting tools available including spark plug wrenches, oil checking equipment, and fuel testing supplies. Simple diagnostic procedures can identify problems quickly and prevent extensive damage.
Document problem symptoms and conditions when issues occur. Detailed descriptions help service professionals diagnose problems more efficiently and reduce repair costs.
Maximizing Equipment Value Through Proper Care
Proper seasonal maintenance is essential for preserving your equipment’s value and extending its lifespan. Well-maintained tools and machines not only retain a higher resale value but also deliver years of reliable service with fewer unexpected breakdowns.
When it comes to small engine care, the quality of maintenance matters more than the hours of operation. Engines that receive consistent seasonal care can outlast neglected ones by decades, proving that an investment in high-quality maintenance pays off in reliability and durability.
To keep your equipment running smoothly, follow the manufacturer’s recommended maintenance schedules and use quality parts. Skipping these steps or cutting corners often leads to costly repairs and a decline in equipment value.
Combining professional maintenance with regular owner care strikes the perfect balance between cost and reliability. This proactive approach ensures your equipment is always ready when you need it most, maximizing both its longevity and your investment.